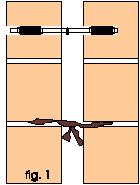
|
|
HISTORY |
Cavity walls incorporating metal ties have been in use since the beginning of the nineteenth century but it was the 1930's building boom that produced large numbers of cavity construction dwellings. From 1945 cavity wall construction became the normal for houses and many other buildings.
|
The early metal ties produced mainly from wrought or cast iron performed satisfactorily but in more recent years mild steel ties have been used and despite galvanising or bitumastic treatments have been found to suffer from corrosion. A British Standard was produced in 1945.
|
The estimated life of these mild steel ties is appreciably less than the 60 year life expected. The 1945 standard was relaxed in 1964 and 1978 but in 1981, when the extent of the problem was registered, the British Standard was amended to triple the zinc coating thickness on a wire tie.
|
A number of cases of distress of cavity walls, attributable to wall tie failure, have occurred in the United Kingdom and it is now clear that the problem could eventually affect all the cavity wall structures built before 1981, some 10 million dwellings, and will not in future be confined only to cases or poorly made ties.
|
Wall tie failures reported to the Building Research Establishment (BRE) include inferior coatings of bitumen, insufficient zinc galvanising on mild steel, aggressive mortars (particularly black ash), exposure to marine climates and permeable mortars such as lime that permits rapid carbonation.
|
It is estimated that over 3 million houses of cavity wall construction were built before the introduction of the 1945 standard. Between 1945 and 1964 an additional 3 million houses were built to the British Standard BS 1243-1945 with a wire tie life expectancy of 15 to 31 years and a strip tie life expectancy of 31 to 61 years. From 1964 to 1986 over 4 million houses were built to the lower British Standard with a tie life expectancy of 23 to 46 years.
|
It was estimated in the 1986 Survey of English Houses that around 12 million properties exist with cavity walls of which the number requiring some repairs to wall structures is approaching one million.
|
|
Corrosion. |
Tests have shown that the rate of corrosion of the protective coating is more rapid in the damp outer leaf that in the drier inner leaf. Average zinc loss in the outer leaf of 15 g/m2 compares with 6 g/m2 in the inner leaf giving in the case of a wire tie a predicted life in the outer leaf of 12-26 years compared with 43 years in the inner leaf.
|
In 1979 it was predicted that 50% of the wall ties in pre 1939 properties could have failed. There are no statistics for bitumen coated ties but flaking by underfilm corrosion at pin holes in the coating appears to occur at a rate comparable to zinc coating.
|
It is quite clear that deterioration of the coating is faster in a damp wall without consideration to outside factor such as chemical additives to mortar, marine salts and industrial atmospheric pollution. If cavity wall insulation restricts the drying of a wall by preventing evaporation this could also contribute.
|
Once the steel of the wall tie is exposed to air and oxygen, the all too familiar rusting cycle begins. The rate of corrosion will be governed by site conditions but in severely exposed locations the life of the twist tie could be reduced to ten years.
|
The loss, by corrosion, of the wall tie is one problem but the other consideration is the rust lamination that can cause the volume of the steel to increase to four times its original thickness. The effect of this is to cause splitting at mortar courses and the lifting of the outer leaf of the cavity wall without necessarily affecting the inner leaf. The result is instability with the affected wall moving out of plumb. |